Innovative biomaterials have been edging into the consciousness of businesses and consumers for some time, yet hesitations from both sides are delaying them from becoming mainstream.
“The barrier is the infrastructure”, says Shellworks co-founder and CEO Insiya Jafferjee, as she talks with Atelier Luma’s material designer Henna Burney as part of London Design Festival’s Global Design Forum. In their roles at the packaging and research company (Shellworks) and France-based design and research lab (Atelier Luma), Jafferjee and Burney work at the intersection of design, science and engineering and recognise that a cross-disciplinary approach is necessary to take new materials from concept to reality.
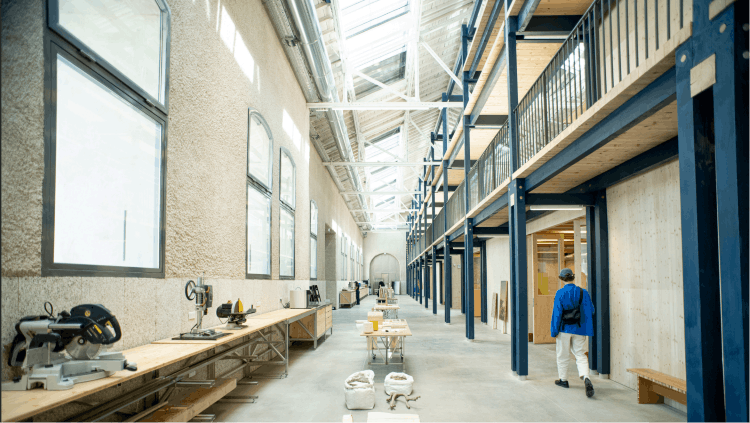
In the context of their most recent projects, the pair discuss how current materials, supply chains and production systems can be redesigned, making way for new, more sustainable materials.
Antibacterial crystalised salt door handles
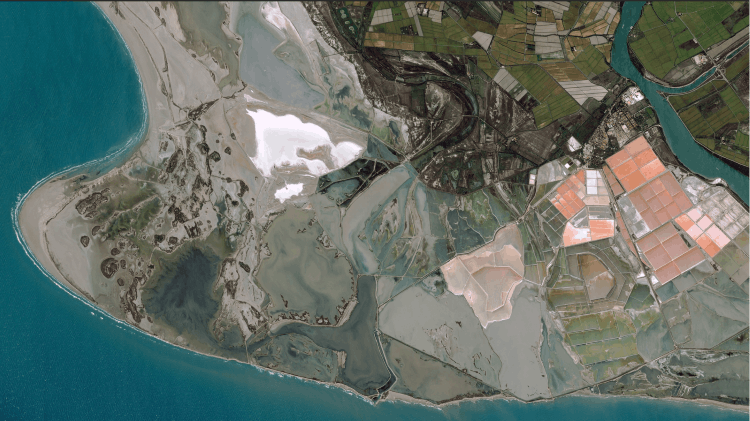
In Arles, a city located on the Rhône River in the south of France, Colombian-born Burney develops new biomaterials from wood, metal, salt and algae. Just 30 minutes away from Atelier Luma is the Camargue region, which is home to vast, 100-year-old manmade salt marshes.
Sea water from the Mediterranean Sea – which has a very high concentration of salt – is pumped into the marshes, where the salt concentration increases to the point of supersaturation. The marshes produce more than 400,000 tonnes of salt every year and the biodiversity in the area depends on the high saturation, so the marshes are carefully maintained.
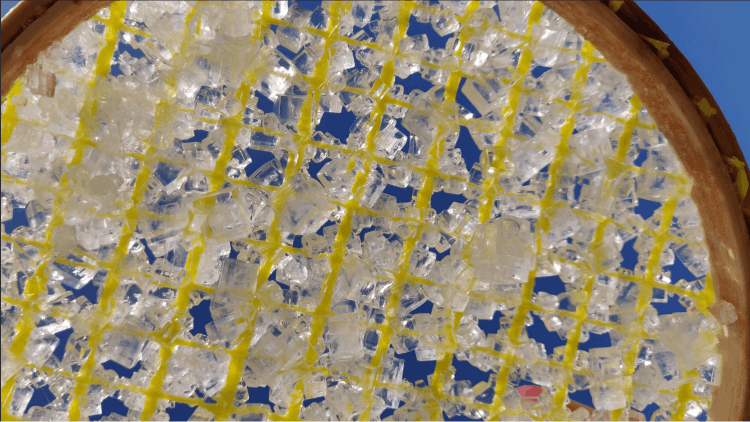
In 2017, Atelier Luma began researching salt and its crystallisation process. Burney describes it as a “natural additive manufacturing process”, whereby crystals “attach to the substrate” in layers and continue to build up. Custom-made metal perforated sheets are submerged underwater in the salt marshes for around ten days, as salt crystals grow all over their surface.
After finding that glass-like panels could be produced from the salt, the research lab’s funding body, the Luma Foundation, wanted to use them to clad the walls on the ninth floor of its Arles Tower building. Since no company existed to make these panels, Atelier Luma had to formalise its prototyping process into a production line able to make 4,600 panels to cover 500 square metres. This involved talking with locals familiar with salt crystallisation to design the bespoke process, including working out the perfect time and positioning to crystalise the panels, according to Burney.
During Atelier Luma’s research, Burney found that salt has many useful properties, including the fact that it is naturally antibacterial. Thinking about a real-world design application for this, Luma Atelier developed door handles made out of salt as, according to cleaning experts, door and cabinet handles carry on average 3,200 different germs.
While salt handles would kill most of the bacteria, they would also erode over time. With this in mind, Luma Atelier devised a cartridge system, so that the salt element of the handle can be replaced when needed. Around 25 door handle prototypes are now in use within the Atelier Luma building and the team is currently testing the lifespan of each salt cartridge.
Burney also notes its aesthetic properties, as salt crystals are translucent and can “diffuse light”. As well as the panels and door handles, Atelier Luma is also looking at designing lamps with the salt.
Packaging “made and unmade by microbes”
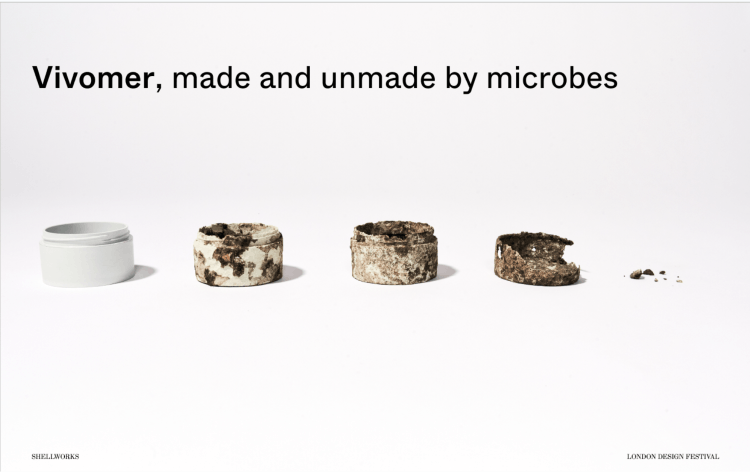
Jafferjee – who previously worked at Apple as a manufacturing design engineer – defines Shellwork’s vision as “materialising a better future by eliminating plastic waste”. The company has been working on a material called Vivomer for the last four years, which she says is “made and unmade by microbes”.
Vivomer is a 100% vegan, compostable mono-material and is made with microorganisms found in marine and soil environments adapting fermentation methods common to the food industry. Jafferjee explains how, because it is created by microbes, “those same microbes recognise it as food when you throw it away” so, although it starts out as a “robust” material, it can biodegrade in around 16 weeks.
Shellworks targeted the beauty and cosmetics industry with Vivomer, as most cosmetics packaging uses five different materials, making it “fundamentally unrecyclable”, says Jafferjee. She believes that, as skincare and makeup companies have started to think more about ingredients, they have also started to seek eco-friendly packaging solutions.
With most packaging, the challenge lies in recycling, as it is made using many different materials all with different “ends of life”, according to Jafferjee. With vast amounts of microorganisms at our disposal comes the possibility of creating “different types of material systems all with the same end of life”, she says.
“It’s not enough to be sustainable”
“Conventionally, applications have been developed linearly”, says Jafferjee, meaning you start off with the application and then choose the materials, but to create new systems designers need to turn this on its head. Evolved design processes might involve “going back to the design and tweaking it” constantly as well as “creating materials that last only as long as they need to”, she adds.
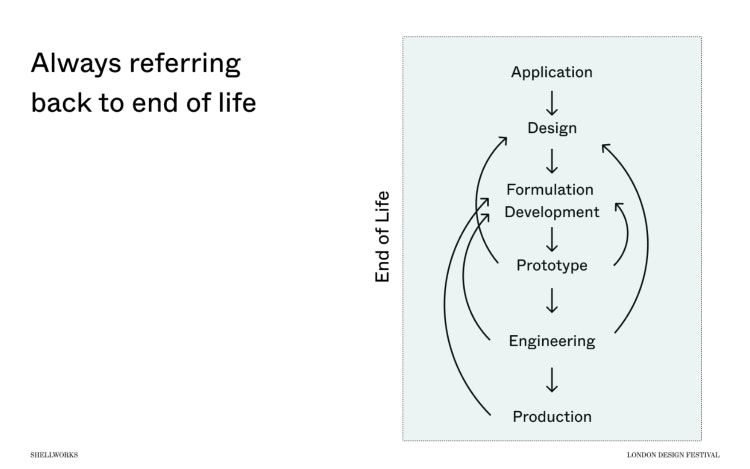
Jafferjee recognises the importance of working in “the commercial as well as the natural” as success also depends on being “cost competitive and performant”. Especially in the cosmetic industry, biomaterials must be able to withstand different environments, such as wet or damp environments.
Trying to create a system that works within existing manufacturing processes is one way to ensure that a material will be commercially viable, while designers must also consider how to make it “future proof”, so it doesn’t create more problems, says Jafferjee.
“Proving that it’s possible”
Materials created from microbes have been around since the 60s, Jafferjee reveals, so why is it taking so long for them to enter mainstream production?
“It takes time and a lot of it is driven by consumers and what we care about”, she says, adding that there is “a lot of fear around this transition” on the business side, which is why we “aren’t able to scale and push these solutions through”.
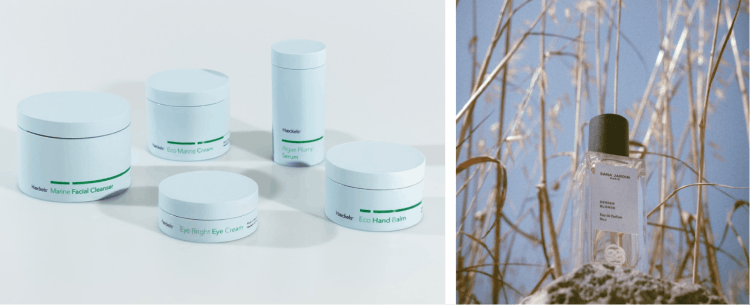
Shellworks tries to communicate that “what might seem like a big risk today is perhaps something worth trying” and Jafferjee believes she is “starting to see a shift” in consumer behaviour. She also thinks “there will always be some form of reuse and recycle” but that organic and chemical recycling should become “part of the vocabulary” rather than just mechanical recycling.
Atelier Luma has started to work on exhibitions to introduce new materials to those outside of the industry as “sometimes it feels like the new material era is only for designers”, says Burney. She identifies the challenge as “proving that it’s possible”.
“We know salt as being something for consumption, but we don’t know salt as a material, so we need to transmit this knowledge and show the possibilities,” she explains. Retaining the aesthetic of a regular door handle was important, according to Burney, so users would be familiar with the form already and therefore more likely to embrace it.
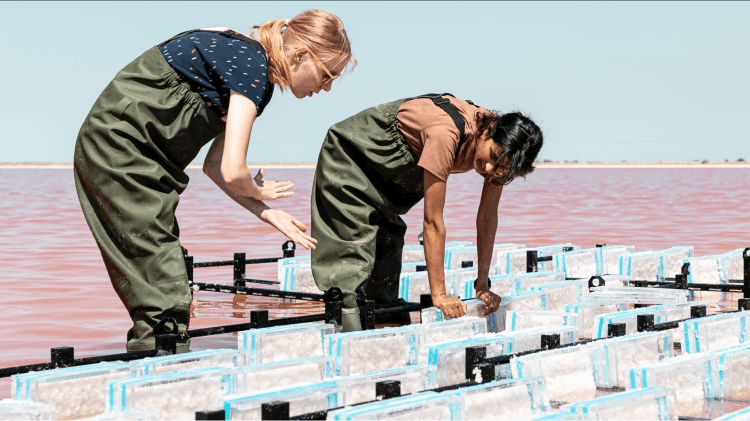
- Design disciplines in this article
- Industries in this article
- Brands in this article