Walking among the exhibitors at Materials Matters 2023 is like taking a glimpse into the – hopefully near – future. From abstract mushroom lamps to batteries made of tyre particles, the trade show invites visitors to consider how new materials might fit into our lives as well as how we can repurpose those that we already use.
Housed by the Bargehouse in Oxo Tower Wharf, each floor has its own sub-theme. Projects on the first floor could be described as experimentalist, with most of them still being at the research stage while the floor above is dedicated to aluminium manufacturer Hydro and other clean-tech companies. Market-ready design products that show material innovation have taken over the third floor, while the loft space showcases a roster of designers, makers and smaller manufacturers working with a variety of materials.
Hemp in the home
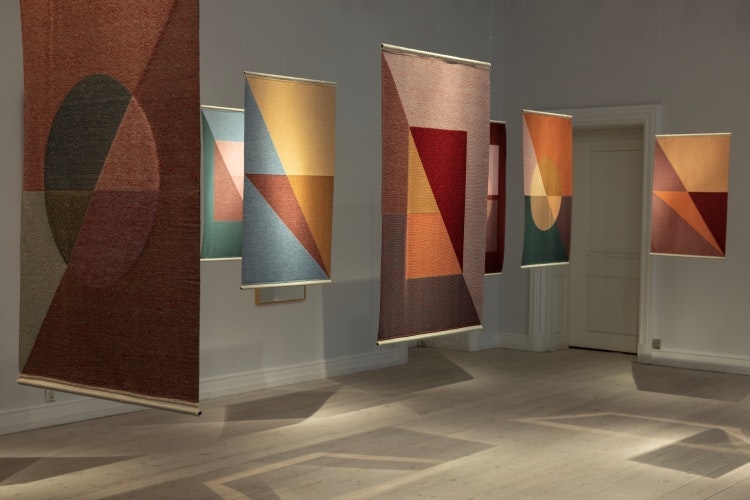
Hemp makes an appearance in the show from the outset through an installation of woven pieces by Danish textile designer Tanja Kirst suspended from the ceiling. Kirst came across hemp while doing an internship in Japan and studying at the Royal Academy.
While Kirst has worked with hemp for around seven years, the Planted exhibition at Material Matters marks the first time that she has combined the material with pineapple fibre, citrus fibre and seaweed. She notes that hemp plants have a “very high yield potential”, as each part of the plant can be used for different purposes but, to make the yarn for her weaving, Kirst uses fibres from the stem.
Despite only using seven different yarn colours, you can see many more hues in the Planted installation, achieved by combining colours to make new ones. On the larger textile towards the back of the entry space, there is an example of the swatches made by Kirst, which amounts to almost 100 different shades.
She sees a place for hemp in the interior world, as it could be developed into rugs and upholstery textiles and might even work in the fashion industry.
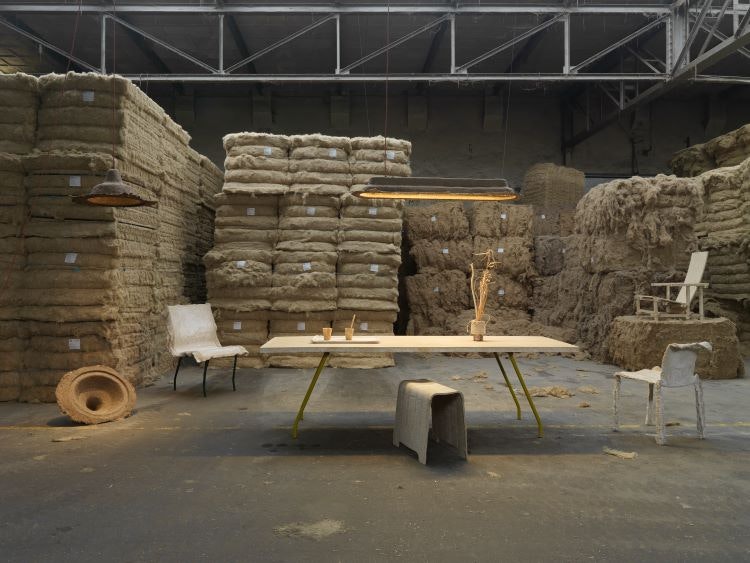
Up on the experimental floor, designer and researcher Jack Brandsma is exhibiting hemp in quite a different way, demonstrating how it can hold its shape as a 3D form with tables and chairs. The origin story of Material Magic unearths how hemp’s sustainable properties are being compromised as it starts to appear in consumer products, while the pieces on show aim to prove that there is a better and equally effective method available.
Netherlands-based manufacturer Hempflax produces hemp fibres, specifically hemp felt. When Brandsma found the company, he noticed that a lot of hemp felt gets sold to the automotive industry for use in door panels and other parts. While he initially thought it might be for “green reasons”, he found out that it was favoured by automotive companies because of its lightweight properties and that it was being fused with a “synthetic binder”, making it impossible to recycle.
In a bid to find other ways the to bind the material while retaining its sustainable properties, Brandsma found two companies not far from Hemflax. One produces potato starch and the other magnesium, both of which can be combined with hemp to make a durable 3D shape.
Material Magic is an example of how we can reproduce design classics in new materials, as Brandsma feels it is “better to replace certain materials in existing products” to demonstrate how it can be applied in the real world. Brandsma is looking at how people respond to the material at Material Matters sand other fairs to work out how to take it forward.
Reframing existing materials
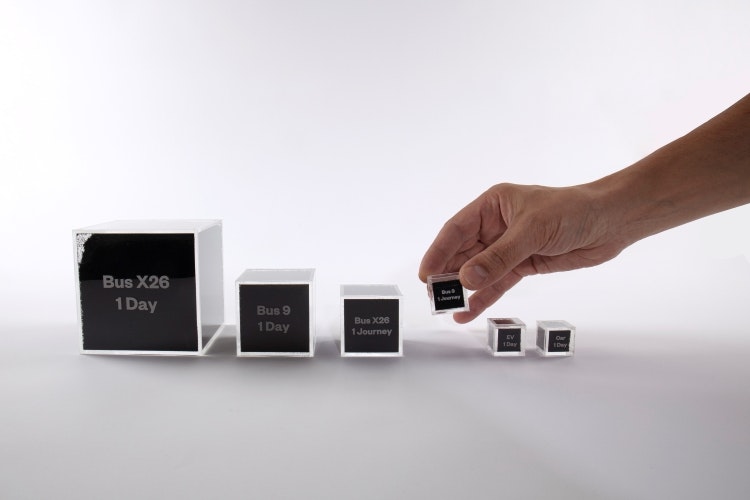
Over a million tonnes of tyre wear particles are produced annually in Europe and they are the second largest microplastic pollutant in our oceans, according to clean tech start-up The Tyre Collective. Although much of the focus in cities like London is on exhaust pollution with many believing electric vehicles (EVs) to be the solution, the company also reveals that the air in London contains more tyre wear than exhaust pollution and the problem if being exacerbated by heavy EVs.
In response, The Tyre Collective has developed a first-of-its-kind device to capture tyre particles at the source using electrostatics and airflow, but how do we dispose of these harmful particles once we have captured them? The answer is you don’t.
The collective’s exhibition looks at ways we can repurpose the material and give it a second life. A sleek, 3D printed acoustic panel made from 20% tyre particles and recycled PLA adorns a wall in the space, while display tables demonstrate how carbonised tyre particles can be used in batteries and pressure senses.
Bill Amberg Studio has worked with leather for over 30 years and its founder and namesake has witnessed the materials decline as it suffers with “an image problem” due to the industry’s “complacence”. Amberg hopes to “reintroduce” leather back into the material conversation as he believes it to be “an extraordinary renewable resource” with “biodegradable and repairable” properties.
Working with an estate in Sussex, England, which has recently been rewilded – meaning fences were taken down to let animals roam free year-round to allow biodiversity to thrive – Bill Amberg Studio designed and made furniture for the on-site restaurant using skins from the cattle on the estate. Amberg thinks Material Matters is “the perfect opportunity to talk about circularity and regenerative farming”, highlighting that the studio waits for the cattle to be killed for meat rather than killing for materials, as well as “utilising every piece of the hide”.
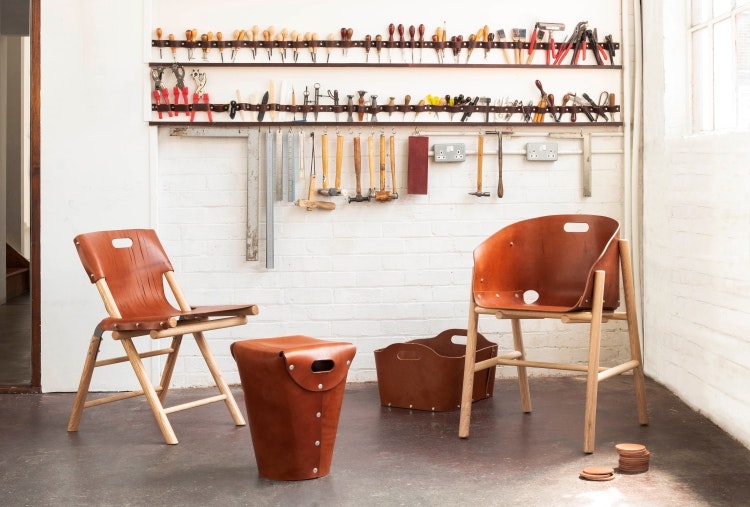
The studio also uses a vegetable tannery technique on skins, which Amberg claims is “the oldest continuing industrial process that mankind has ever done”, with vegetable tannery sites in France going as far back as 30,000 years.
While vegan leather alternatives, like apple leather and pineapple leather, do exist Amberg reveals that pineapple leather is actually 40% plastic and apple leather is 60% plastic, making them “irreparable and not nearly as durable as leather”. He plans to continue adopting circular, regenerative methods, using leather for drinking vessels and even combining it with hemp.
Responding to climate change
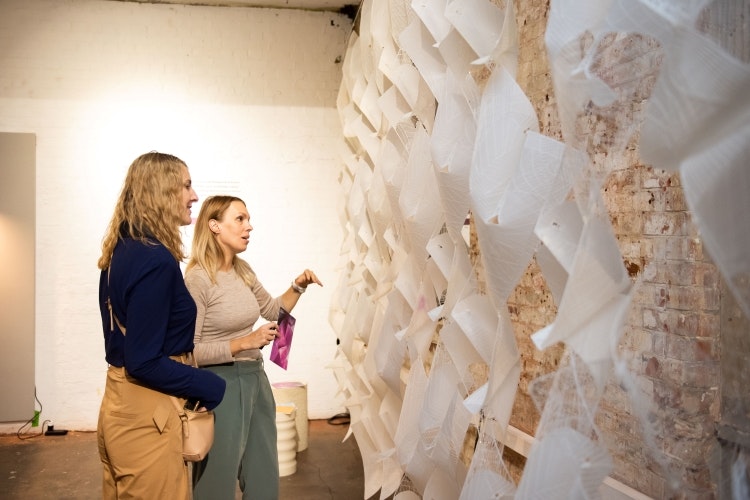
Bioplastics are one of the more well-known categories among new materials and feature throughout Material Matters, but one installation stood out above all others. An impressive structure of folding, twisting lattices encompassed one side of a room on the first floor of the Bargehouse which, upon first glance, looks like a pretty installation but as it was exposed to UV light, it began to change from brilliant white to a pink, before darkening to a shade of purple.
Sensibiom 2.1 was designed by Crafting Plastics and DumoLab Research and works by responding to UV radiation. The Nuatan bioplastic structure holds an environmentally responsive skin that self-stains in ten different shades to signal real-time changes in UV solar radiation.
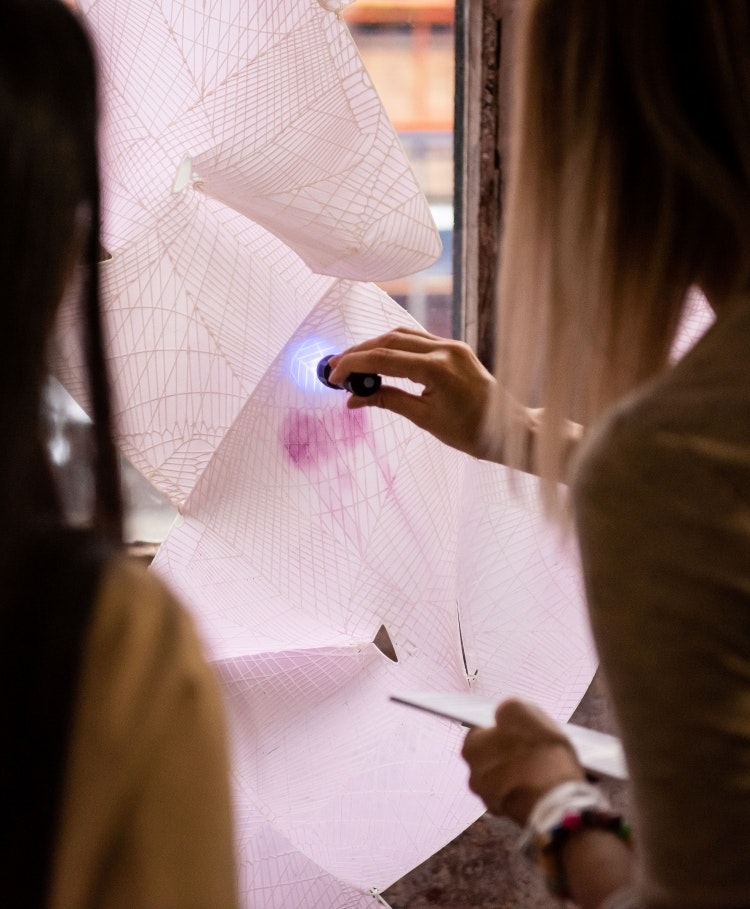
Since global UV radiation is on the increase and can cause damages to skin, eyes and even DNA, Sensibiom 2.1 could be used both indoors – as most UV rays can penetrate clear glass windows – and outdoors to signal the severity of the threat, indicating whether people should use sun protection or even avoid the sun altogether.
Other highlights
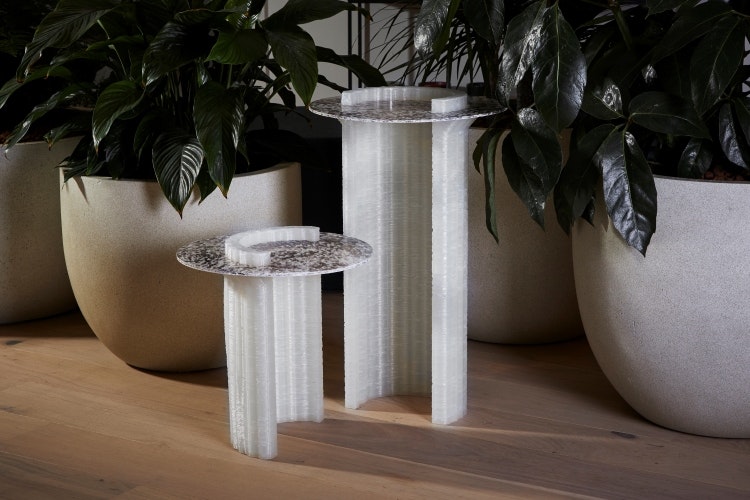
Interior architects HagenHinderdael produce installations, products and furniture pieces, often working with digital fabricators that use robots to print organic shapes. In its latest collaboration, HagenHinderdael has taken its 3D printed sugar made from left over sugar cane and Novavita Design’s food waste and developed a series of coffee tables. The “milk, coffee, sugar” tables have with 3D printed sugar base, coffee waste and milk packaging waste tabletop, according to HagenHinderdael co-founder Sofia Hagen, and are being showcased on the top floor of the trade show.
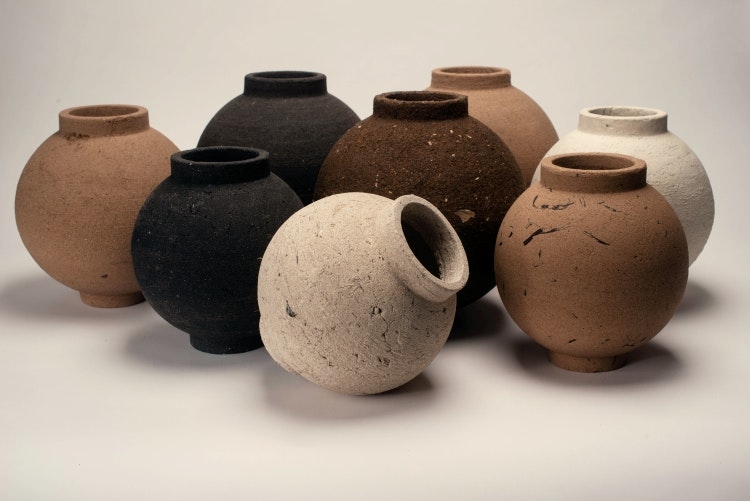
Interpreting the circle of life on a whole new level, Dyingarts founder Simon Frend is exhibiting his Closing the Circle environmental cremation urns. Each is handmade from natural materials, such as sand, ash, cuttlebone, charcoal, and shell, and designed to dissolve in water or gently biodegrade in the earth, returning the materials along with the human ashes to their origin with zero impact.
- Design disciplines in this article
- Industries in this article
- Brands in this article